Saint-Gobain Weber experimenteerde al met het 3D-printen van beton sinds het begin van deze eeuw en realiseerde haar eerste 3D-geprinte muur in 2005. De jaren daarna groeide dit experiment stap-voor-stap uit tot een nieuwe productiemethode in de bouw. Inmiddels rollen er dagelijks producten uit de 3D-betonprinter in de fabriek in Eindhoven. Peter Paul Cornelissen, Business Unit Manager 3D Printing, en Udo Snijer, Productmanager beton, vertellen over de voordelen van 3D-betonprinten en de mogelijkheden die de printtechniek biedt voor de openbare ruimte.
3D-betonprinten: duurzamer, sneller en meer ontwerpvrijheid
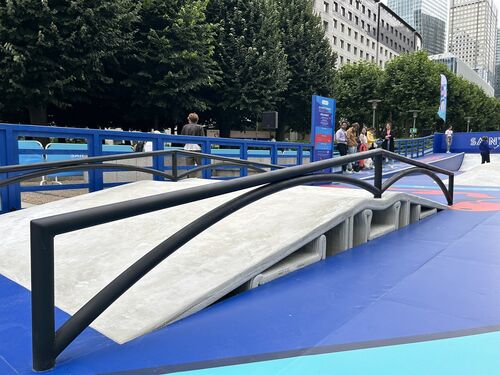
Tekst: Peter Bekkering
Het begin
Cornelissen vertelt hoe 3D beton printen ooit begon: “We kregen begin deze eeuw, vanwege onze expertise op het gebied van mortels, vanuit de University of California de vraag of we een betonmortel konden ontwikkelen om 3D te printen. De basale eis was dat de geprinte lagen, de lagen die er daarna op werden geprint konden dragen. De onderste lagen zijn uiteraard niet direct uitgehard, maar zullen het gewicht van de lagen die volgen op basis van hun reologische eigenschappen moeten dragen. Anders kun je slechts enkele lagen per keer printen, voordat alles in elkaar zakt. Dit resulteerde in de eerste 3D-geprinte betonnen muur in 2005. Hiermee werd aangetoond dat zowel het materiaal als het proces kansrijk waren.”
In 2015 besloot Theo Salet, professor aan de TU Eindhoven, te onderzoeken hoe het 3D-betonprintproces meer geautomatiseerd kon worden. In samenwerking met onder andere Saint-Gobain Weber en BAM Infra werd in 2017 de eerste 3D-geprinte fietsbrug bij Gemert gerealiseerd. Deze betonnen brug van acht meter werd geprint in het lab van TU Eindhoven. Twee jaar laten besloot Saint-Gobain Weber een eigen productlocatie in te richten. In januari 2019 werd de eerste commerciële betonprintfabriek in Europa geopend in Eindhoven, waar toen een 29 meter lange fietsbrug voor Nijmegen werd geprint. Later zijn de ontwikkelings- en productieactiviteiten in 3D-betonprinten steeds verder geïntensiveerd.
De 3D geprinte fietsbrug in Nijmegen
Het proces
Cornelissen legt uit hoe het proces werkt. “Eerst wordt door middel van 3D-software een ontwerp gemaakt van bijvoorbeeld een brug, trap of constructief element. Dit bestand ontvangen wij van onze klanten. Vaak maken wij dan, samen met de klant, een vertaalslag naar een ontwerp dat geprint kan worden. Dit uiteindelijke ontwerp wordt in laagjes verdeeld. Dit noemen wij het ‘slicen’ van het ontwerp. Deze laagjes worden daarna omgezet in een robotcode, zodat de robot deze laagjes op elkaar kan printen. Zo wordt de digitale vorm opgebouwd tot een fysiek object.”
Weber 3D Mortel Platform
Voor veel bedrijven zit 3D-betonprinten nog in de R&D- en trial and errorfase. Saint-Gobain Weber heeft het 3D Mortel Platform ontwikkeld om de kwaliteit van een eindproduct te kunnen garanderen. Cornelissen: “Dit platform waarborgt het proces, waardoor we structureel en consistent de benodigde kwaliteit kunnen leveren aan onze klanten. We gebruiken droge betonmortel die speciaal voor het 3D-betonprinten is ontwikkeld en volgens het KIWA-certificaat geproduceerd en gecontroleerd wordt.’
“Vervolgens monitoren we het hele printproces door middel van sensoren en kwaliteitsmetingen. Deze generen de benodigde data om het volledige printproces te controleren. Na het printen wordt de sterkteontwikkeling van de geprinte objecten na 7 en 28 dagen gecontroleerd. Pas als het hele Kwaliteit Controle Proces met succes is afgerond, krijgt de klant een certificaat. Hierop staat dat het geproduceerde object voldoet aan alle, vooraf afgesproken, waarden. Met dit hele proces zijn wij uniek in de wereld.”
aint-Gobain Weber faciliteert een volledig gedigitaliseerd proces, waardoor de foutmarge afneemt, de objecten snel geleverd kunnen worden en de werkzaamheden op locatie significant gereduceerd kunnen worden. “Een ander belangrijk voordeel is dat je vanwege de robotisering veel minder mensen nodig hebt. Belangrijk in een tijd van personeelsschaarste in de bouw.”
3D geprinte taludtrap in Amstelveen
Wereldleider in licht en duurzaam bouwen
Weber is onderdeel van Saint-Gobain; wereldwijd leider in licht en duurzaam bouwen. Saint-Gobain ontwerpt, produceert en distribueert materialen en diensten voor de bouw en is actief in 76 landen. Snijer legt de toegevoegde waarde uit van Weber als onderdeel van Saint-Gobain. “Dat zit in het delen van kennis op het gebied van equipment, mortels en technologieën.” Cornelissen vult aan: “We hebben wereldwijd de meeste kennis en praktijkervaring op het gebied van 3D-betonprinten. Kijk maar naar alle producten en projecten die inmiddels gerealiseerd zijn. Dan heb je het onder meer over zo’n 50 à 60 taludtrappen, zes bruggen, de huizen van project Milestone, skateparken en verschillende torens. Dat alles heeft ons een schat aan kennis en ervaring opgeleverd over materiaal, proces en de benodigde eindkwaliteit van constructieve producten.”
Materiaalbesparing
Er is een groot verschil tussen de traditionele manier van beton storten en het 3D-printen van beton. Cornelissen: “Bij de traditionele manier werk je met een mal waar eerst wapeningsstaal in wordt gelegd en vervolgens beton in wordt gestort. Bij 3D-betonprinten printen we alleen beton waar dat nodig is. We printen de contouren en indien het voor de sterkte nodig is, printen we tegelijkertijd in de holtes een structuur om de krachten te kunnen dragen. Dit resulteert bij projecten in een CO2 reductie van 50 tot 70 procent.”
Saint-Gobain Weber gaat daarnaast nog verder op het gebied van duurzaamheid. Snijer: “We onderzoeken of we het cement in betonmortel geheel kunnen vervangen. De eerste stap daarin is gezet met Weber 3D Eco, een product met 49 procent minder CO2-uitstoot dan de traditionele mortel. Bij deze ontwikkeling bouwen we verder op de enorme kennis die beschikbaar is binnen Saint-Gobain Weber Beamix.”
Vormvrijheid
Vrijwel alle vormen kunnen eenvoudig worden geprint. Ook vormen die door middel van traditionele bekistingen vaak onmogelijk waren. Zo kun je probleemloos dertig skate-elementen maken en die allemaal iets laten variëren. Dat is bij traditioneel gestort beton onbetaalbaar. Cornelissen: “De mogelijkheden zijn overigens niet grenzeloos. Elke technologie heeft zijn beperkingen, ook 3D-betonprinten. Bovendien doen we geen concessies aan de kwaliteit.”
Bijvoorbeeld voor straatmeubilair ziet hij grote mogelijkheden: “Daarbij zijn optimalisatie per locatie, personalisatie en ontwerpvrijheid - vooral met organische vormen - de voornaamste voordelen. 3D-betonprinten is een perfecte bouwmethode als er allemaal unieke vormen of afmetingen nodig zijn. Het toverwoord hierbij is parametrisch ontwerpen. Dat is een proces waarbij modellen of ontwerpen automatisch worden gegenereerd op basis van parameters, zoals maten, materiaaldikte of geometrie. De printrobot kan eindeloos variëren op basis van verschillende parameters.”
Acceptatiecurve
In de markt van de openbare ruimte wordt 3D-betonprinten steeds vaker toegepast, zegt Cornelissen. “Het is een technologie die door de markt omarmd moet worden. Als je kijkt naar de acceptatiecurve van nieuwe producten of technologieën zit je bij de meeste 3D-geprinte producten nog aan het begin. Bij onze 3D-geprinte taludtrappen zijn we al verder, deze worden al met grote regelmaat besteld. Er zijn steeds meer klanten die het als kans zien om hier vandaag mee aan de slag te gaan, dit zijn echte early adapters. Een voorbeeld is de gemeente Eindhoven, waar we The Vibe voor hebben geprint. Een multifunctioneel openbaar object gebaseerd op de iconische vorm van het stadslogo.”
Multifuntioneel project met stadslogo The Vibe in Eindhoven
Projecten
Een recent fraai uithangbord voor de mogelijkheden van 3D-betonprinten in de openbare ruimte is ook het skatepark van 400 vierkante meter aan de Esplanade de Paris La Défense in Parijs, dat tijdens de Olympische Spelen voor iedereen toegankelijk was. Cornelissen: “Het werd gerealiseerd door Saint-Gobain (Frankrijk) als sponsor van de Olympische spelen. Een aantal skate-elementen voor het skatepark werd vooraf door vooraanstaande skaters en influencers getest in de 3D-betonprintfabriek in Eindhoven.”
Er zijn nog veel meer spraakmakende projecten te noemen. Op de website van Weber is een kaart te vinden met verschillende projecten die inmiddels zijn gerealiseerd door middel van de 3D-printtechniek. Nu er al een flink aantal mooie voorbeelden zijn, willen Cornelissen en Snijer de komende periode gaan werken aan de groei van 3D-betonprinten in de Benelux. Cornelissen heeft er alle vertrouwen in: “Zeker bij straatmeubilair gaan opdrachtgevers steeds meer de voordelen ervan inzien.”
Weber Saint-Gobain
Eindhoven
040- 259 79 00
www.nl.weber
Meer artikelen met dit thema
Gerecycled meubilair voor dakterras Rijkswaterstaat Haarlem
8 jul 2024In Haarlem is een oud pand van de FIOD verbouwd tot een modern en duurzaam kantoor voor Rijkswaterstaat. Het…
Universiteit Twente innovatief met duurzaam buitenmeubilair
18 jun 2024Onlangs is het buitenmeubilair op de campus van de Universiteit Twente vervangen en uitgebreid. De enige echte…
3D-geprint straatmeubilair biedt veel voordelen
17 jun 2024Het 3D-printen van betonnen straatmeubilair en skate-objecten blijkt veel voordelen te bieden. “Je hebt een…
KLARA banken: elegantie in de buitenruimte
27 mei 2024Maak kennis met de KLARA banken-serie: elegant en slank vormgegeven banken en boombanken, die onderling perfect…
Het belang van straatmeubilair: verrijken en verbeteren van de leefbaarheid
29 apr 2024De noodzaak van een goed functionerende buitenruimte, met voldoende zitmogelijkheden, groen en veilige en…
Design Pixel overkapping voor het Alrijne ziekenhuis Leiderdorp
4 apr 2024Op het terrein van het Alrijne ziekenhuis in Leiderdorp is een prachtige Pixel fietsenstalling voor het…
Mooi fietsparkeren bij de Meelfabriek in Leiden
27 mrt 2024De Meelfabriek, opgericht in 1884, deed ooit dienst als een stoommeelfabriek. Na de Tweede Wereldoorlog maakte…
Fila banken op het dak van een appartementencomplex
21 mrt 2024Groen vervult een belangrijke rol in de buitenruimte waarin we leven. Een groene omgeving is niet alleen mooi…